Throughout this semester, the Upper School Science Teacher Travis Menghini’s Engineering class has been working on two projects: railed transportation and bridge design. Students, parents, faculty, and staff were invited to view the railed transportation models and a demonstration of bridge capabilities (that necessarily resulted in each bridge’s dramatic and memorable destruction).
For their transportation project, students had to CAD and build a model of a railed transportation vehicle and track. Examples include gondola lifts, roller coasters, vending machines, and other great projects. They needed to consider where the vehicle and track would be located in the world, its purpose, and any historical or environmental context. The vehicle wasn’t required to run on its own; it could be a model that, in theory, runs with a motor. They also had to consider whether the vehicle turns or turns around or requires switch tracks, and the largest slope it can travel. Perhaps most importantly, they needed to ensure their track was designed to prevent derailment. Students created dioramas that were available for visitors to view at the end of the semester.
For their other final project, students were challenged to employ the engineering design process to construct an amazingly strong, lightweight, one-of-a-kind bridge. They conducted research, and then went through a series of design, testing, redesign, retesting, and ultimately, a final bridge build that complied with all of the criteria and constraints. Each bridge spanned 1 meter (with supports of 20 cm on either end) and was only allowed to be created out of popsicle sticks, Elmer’s glue, and yarn. All the supplies had “costs” attached to them, so students had to be budget-conscious as they deliberated on their designs.
As is the case in most real bridge construction projects, student teams were evaluated in several important categories:
Strength: It’s the responsibility of the engineers to ensure that their bridge design is safe. One measure of a bridge’s safety is to determine the maximum live load that the bridge can support. In this challenge, the live load limit will be determined by adding weights to the center-most portion of the Roadway/Bridge Deck until the bridge collapses.
Design Aesthetic: In general, most people prefer an attractive, creative, and inspirational bridge design. If a bridge is strong but unattractive, that design will most likely not be selected over other, more creative designs. The ability to design and build a bridge that is both appealing to the eye and strong is an important consideration. For this challenge, a team of judges scored each bridge on a scale from 1-100 and then took an average of the scores to determine the final Design Aesthetics Score.
Strength (Live Load) to Weight Ratio: Engineers never have the luxury of unlimited funding, time, and talent. Customers are looking for the strongest, most functional, and attractive bridge they can build within their budget and time constraints. In order to determine a score in this category, each bridge will be weighed prior to testing. After the live load is determined, teams then calculated Live Load to Weight Ratio. The larger the ratio, the better!
Strength (Live Load) to Weight Ratio = Live Load (lbs.) ÷ Bridge Weight (lbs.)
For both projects, engineering students were also required to write a technical report to present in class.
Congratulations to the winners! Devon Carruthers ’24, Charlotte Derdeyn ’24, Maggie Gonzalez-Navarrine ’24, Julie Qian ’24, and Zoe Zlatic ’24 designed a bridge that held 755 pounds while weighing 9.125 lbs (for a strength-to-weight ratio of 82.7). They bested the reigning record of 635 pounds on a 9.0125 lb bridge (70.5 strength-to-weight ratio) set in 2019.
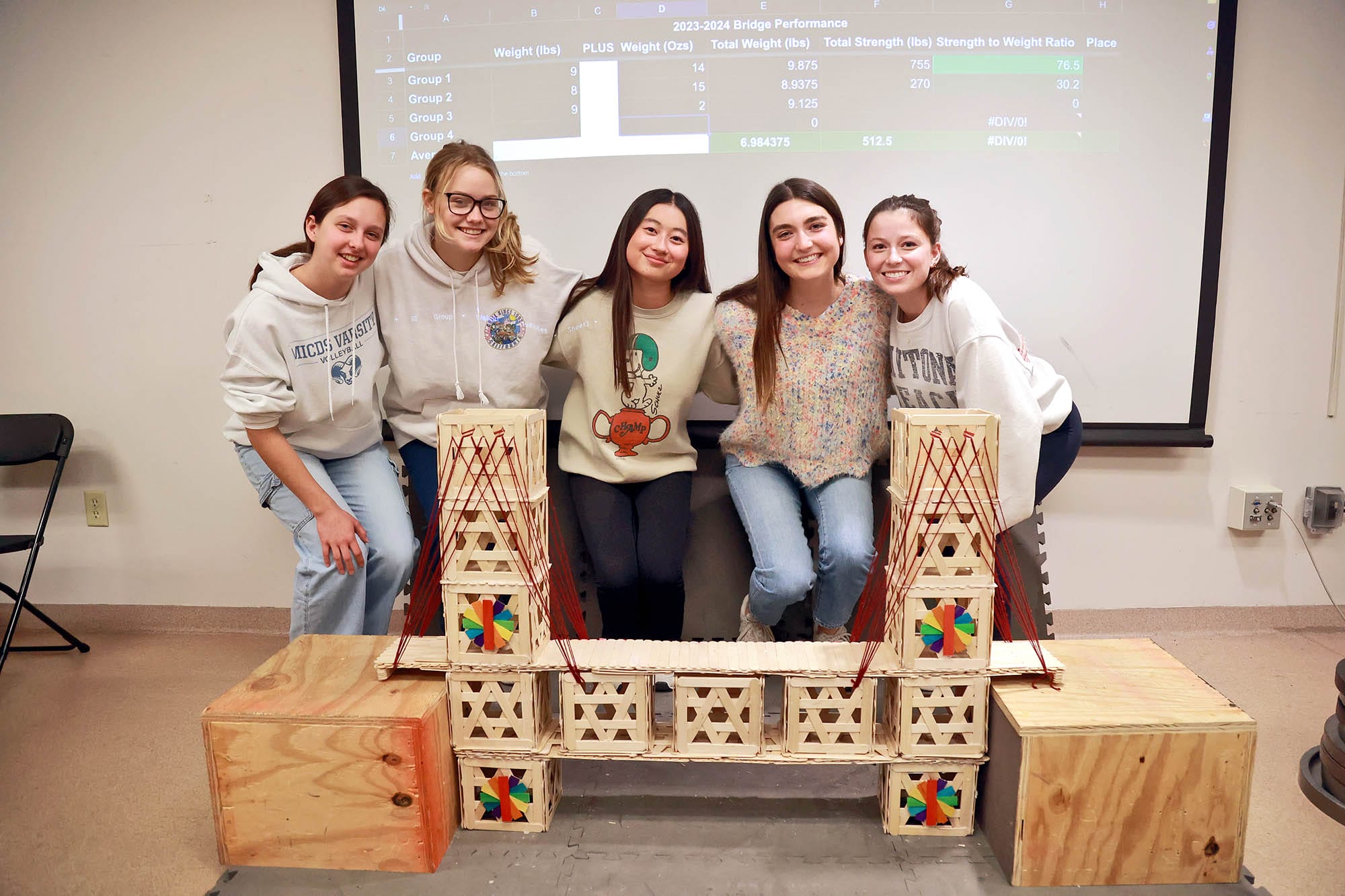
Well done, student engineers! Your projects made for thought-provoking reflection and exciting destruction for our guests.